Federico Rossi: “Después de hacer el primer motor aerospike y de methalox de Europa puedo retirarme”
08/06/2023 Martín Morala Andrés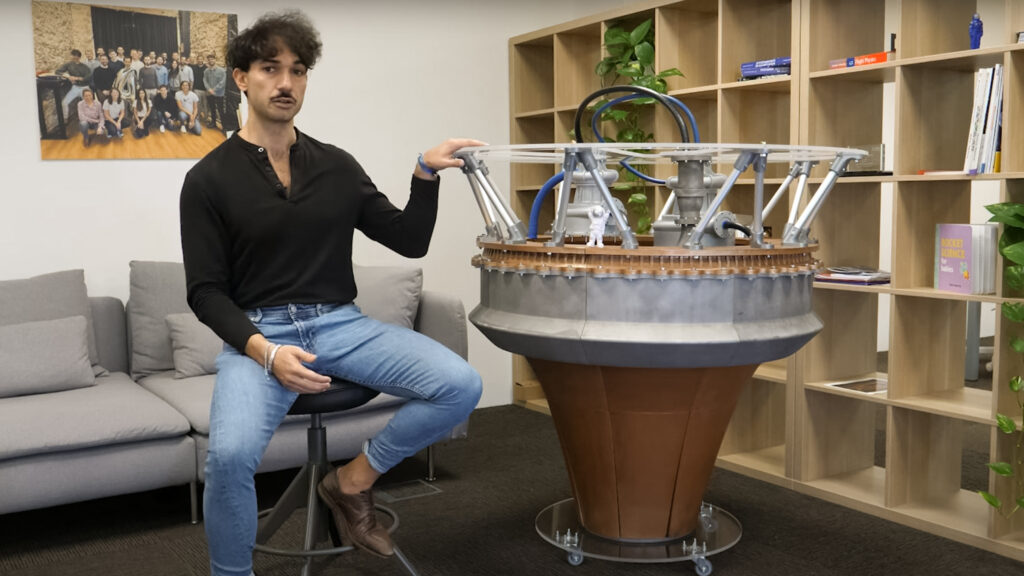
La ingeniería no es un trabajo fácil. Si hablamos de la que está detrás de crear un motor único en el mundo es otro nivel. Simplemente, no todo el mundo está capacitado para trabajar a esos niveles y ni así es un trabajo individual. La cantidad de horas de trabajo, de variables que estudiar y analizar y la complejidad de los problemas que suceden en un motor cohete es única de estos sistemas. Pero entrevistar a todo el equipo era imposible, así que hablamos con quien está detrás de todo, el director de propulsión de Pangea Aerospace, Federico Rossi.
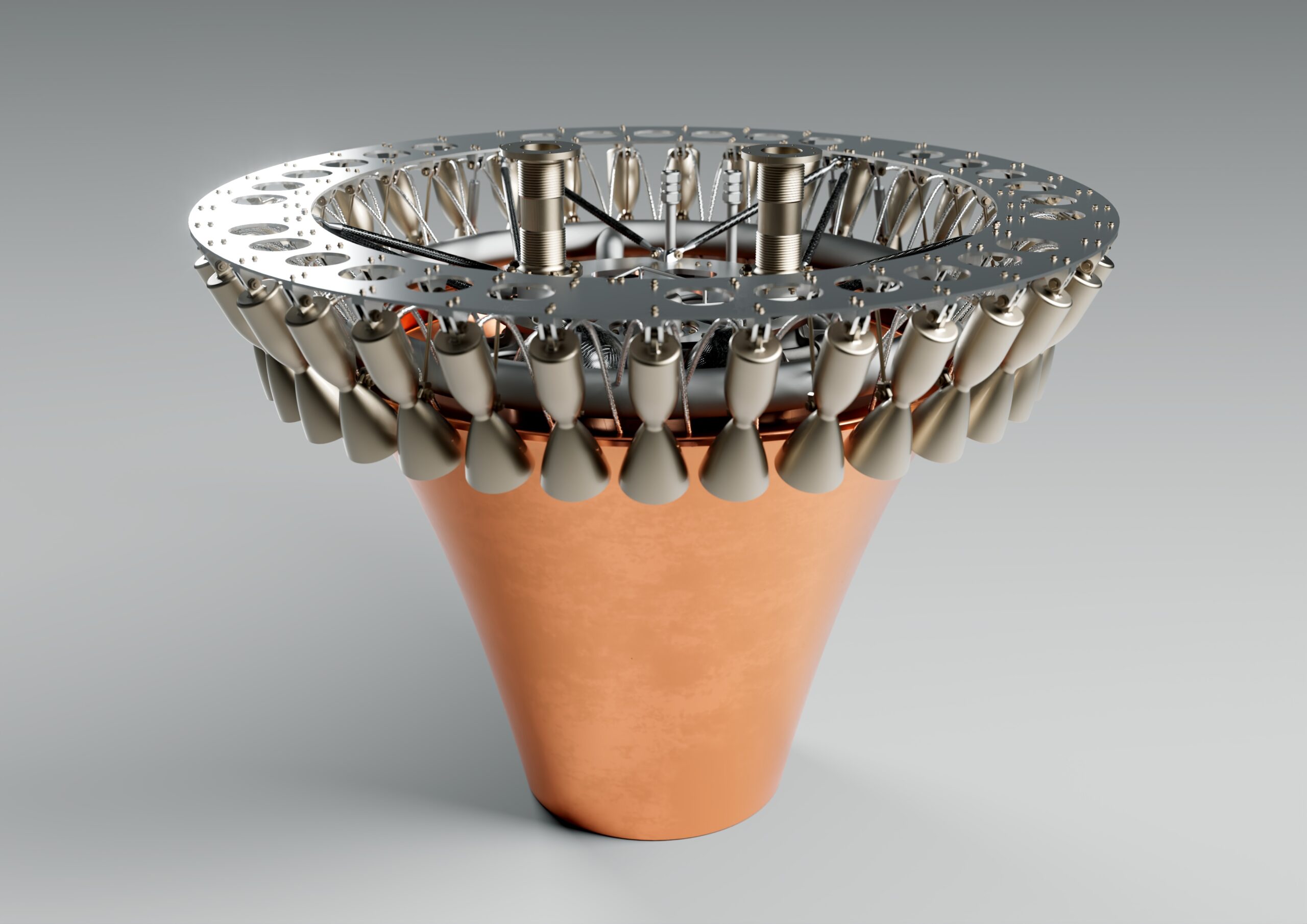
Unos minutos después de hablar con su jefe, el CEO de Pangea Adrià Argemi, nos reunimos con él. Uno de los responsables del éxito de la empresa, además tiene motivos por los que estar contento, acaban de probar el motor para satélites Unyx.
Sin embargo, había que empezar a lo grande.
AstroAventura: Empezamos por lo que creo que es la parte más importante de un motor, la turbobomba. ¿En qué estado se encuentra el desarrollo de la vuestra?
Federico Rossi: Tenemos un equipo de cuatro personas que trabaja en ella. Tienen mucha experiencia en Blue Origin, en General Electrics en turbinas, lo que nos ha permitido a la PDR (revisión de diseño preliminar por sus siglas en inglés) de la turbobomba en solo tres meses. También ha influido un software muy potente que usamos para el diseño.
Ahora estamos en fase post PDR. Estamos analizando en CFD [Compuer Fluid Dynamics, simulaciones de dinámica de fluidos por ordenador] las características off design. Esto sirve para caracterizar la cavitación [fenómeno en el cual en una turbina un fluido líquido se convierte en gas debido a la presión y/o velocidad]. Y vamos a probar los primeros componentes en la segunda parte del año con nitrógeno gaseoso comprimido.
¿Qué diseño habéis optado para la turbobomba, maquinaría eléctrica, convencional? ¿Puedes hablarnos de eso?
Es más convencional, al principio éramos muy fans del eléctrico, cuando empezamos también porque el Meso era más pequeño y teníamos menos potencia en el motor. Ahora que el Meso y el motor han crecido, hasta 300 kN, básicamente, las baterías no pueden aguantarlo. Cuando empezamos había muchas promesas sobre las baterías que no se han cumplido, siguen siendo pobres para esto. Tenemos dos turbobombas de casi 2 mega newton cada una, imagínate las baterías gigantescas que necesitaríamos.
Habéis comentado que las primeras pruebas las realizaréis en la segunda parte del año, entonces de momento, ¿estáis limitados al CFD?
Sí, de momento estamos limitados al CFD y estamos ahora desarrollando los bancos de ensayo, para ver como podemos trabajar en el rango de operaciones extremo.
Tres meses es muy poco tiempo para un PDR, ¿cómo ha influido la experiencia aportada por otros miembros del equipo?
Muchísimo, esto es la clave, tenemos un miembro del equipo que ha trabajado ya en Blue Origin, en Ursa Major también, que es otra empresa en Estados Unidos que hace motores. Y en la parte de la turbina, la más compleja dentro de la turbobomba, otro miembro tiene doce años de experiencia en General Electrics. Allí no trabajó sobre turbinas para cohete, si no para aviación que son si cabe más complicadas.
Otra pata de la mesa es el uso de un software comercial para desarrollarla que está muy bien hecho. Boeing también lo ha utilizado y te permite a nivel de diseño preliminar hacer un desarrollo superrápido de explorar muchas configuraciones al mismo tiempo.
Esto es el espacio, es muy complicado dar fechas, pero, ¿cuándo esperáis tener un primer modelo funcional operativo?
En un año, de las turbobombas.
¿Y siendo más realistas?
En un año y dos meses. Sí, nosotros hacemos cosas rápidas, lo digo siempre, lo que prometemos lo hacemos. Hicimos el Demo P1 el primer aerospike de la historia de methalox, entre cuatro personas y en un año y medio.
El Arcos no usará gas natural licuado, ni siquiera methalox sino bio methalox. ¿Puedes hablarnos un poco de las diferencias entre estos combustibles y porcentaje de pérdida de uno contra el otro?
El gas natural depende mucho de donde lo sacas. En Rusia hay mucho, pero ahora no se puede sacar, también lo hay en Noruega. Entonces, la pureza más o menos es aproximadamente el 98,5%, con el resto siendo propano y un poco de nitrógeno. Mientras que el bio metano, es más preciso porque es siempre el mismo proceso para generarlo, nosotros tenemos un 99,95% de pureza.
¿Fue vuestro departamento el que más impulsó la idea de usar methalox?
Yo diría que sí, nosotros hemos empujado mucho por la reutilización. Es clave y el methalox es, de los hidrocarburos, lo que más te permite reutilizar. El hidrolox podría ser incluso mejor, pero es caro. Además, vuelve el motor muy grande por su baja densidad. Y en un aerospike es fundamental que el motor no se agrande por el propelente.
Uno de los problemas de los aerospikes es que son grandes, eso les lleva a pesar mucho. ¿Cuánto pesa aproximadamente en seco vuestro motor?
Tenemos un target de TWR que es entre 85 y 100. Va a pesar unos 300 o 350 kilos. Pero, también compartimos muchas partes estructurales con el vehículo. Debido a su forma se puede integrar mucho mejor con el resto del cohete y tener una transmisión de empuje mucho más eficiente.
Has comentado un TWR target de entre 85 y 100, eso descontando del Raptor lo sitúa como el mejor TWR del mundo a nivel del mar.
Sí, correcto es un motor muy ligero también gracias a la fabricación aditiva y las aleaciones ligeras. Otra ayuda a bajar el peso es la presión en la cámara de combustión.
¿Alrededor de cuanta presión estáis trabajando ahora mismo?
Menos de 100 bares.
¿Cuánto empuje exacto tendrá el motor?
300 kilonewton a nivel del mar. Tenemos que probarlo, porque nunca se ha probado un aerospike en altura pero estamos convencidos de que podemos aguantarlos para simulaciones CFD. No puedes fiarte solo de las simulaciones, pero son muy buenas hoy en día y te dan una buena intuición de lo que va a pasar.
¿Por qué no combinaciones de motores? Sigue siendo una de las cosas que más me extraña de vuestra aproximación.
De hecho, nosotros tenemos un cluster al final. Si ves el anillo, esto al final funciona como un cluster. Te permite ser mucho más flexible, además, cada uno de estos módulos [señala la pieza adjunta debajo] son la parte más complicada del motor se puede producir más en serie lo que los hace más baratos.
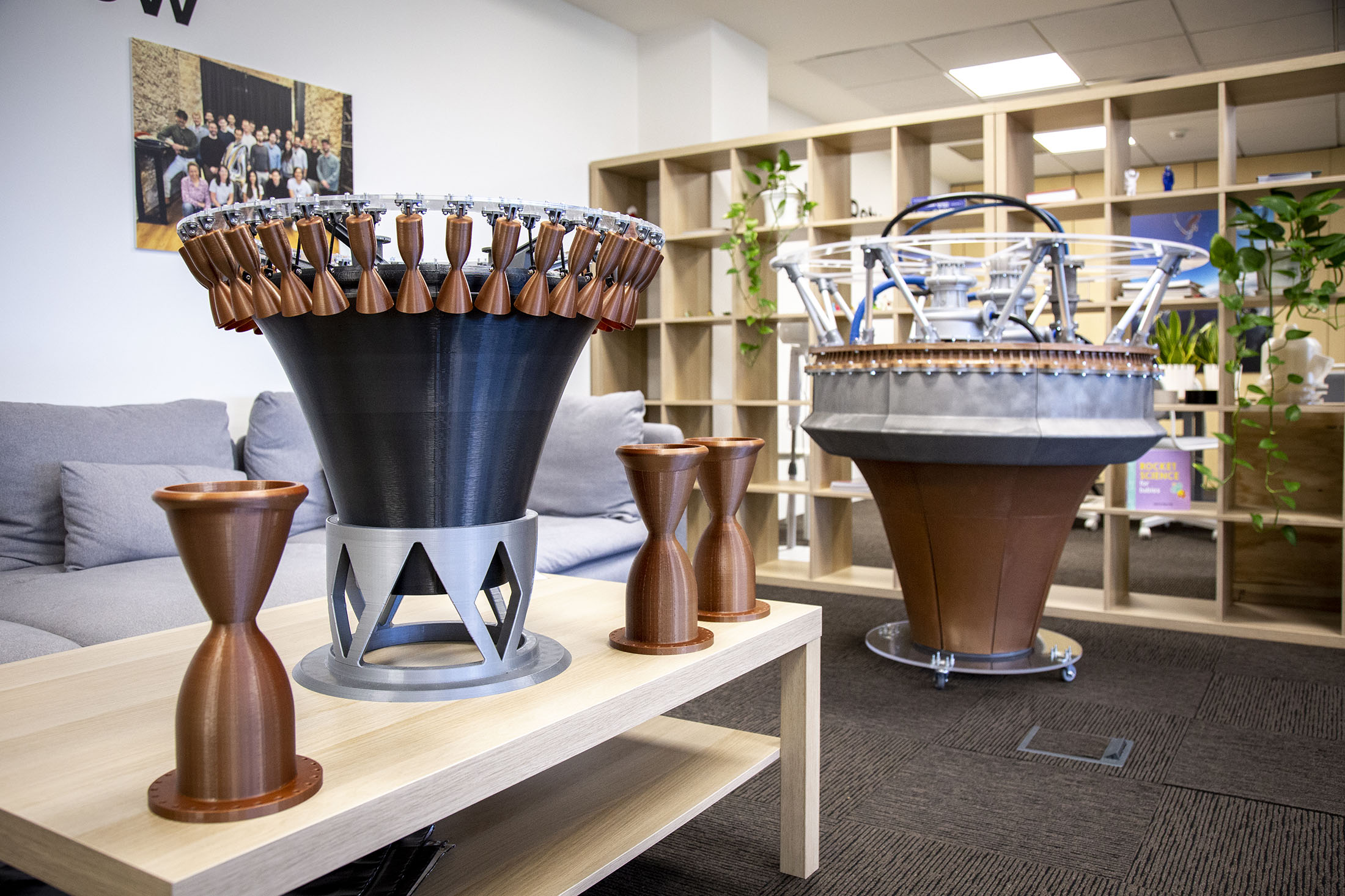
¿Cómo se siente al ser el desarrollador del primer motor aerospike de toda Europa?
Muy bien, de las mejores cosas es cuando estudiaba el tema y leía papers de aerospikes. Porque aquí en Europa se han investigado mucho y hay nombres muy importantes. Y después de las pruebas de Demo P1 que estas personas vinieran y me hicieran las preguntas a mí fue genial. Después de las pruebas pensé, me puedo jubilar, todo lo que haga a partir de ahora es de más.
Pero no habéis sido los únicos en construir y probar un motor de aerospike en Europa sino también los primeros en construir y probar un motor de methalox en Europa…
Correcto. Eso para mí, es también un reto grande, pero tengo que decir que siempre ha sido natural para nosotros. Como no teníamos gente con experiencia en motores con queroseno no era una decisión arriesgada. Además yo he estudiado toda mi vida en Italia, que el methalox está muy fuerte, hay mucha investigación. Y además trabajé con el motor M10 de Avio que usará este combustible.
Volvemos un poco sobre las preguntas técnicas, ¿cómo se ignicia el motor?
La ignición se hace con augmented spark igniter, que es básicamente un pequeñísimo motor cohete que está dentro del motor que lo enciende que va con los mismos propelentes, oxígeno y metano pero gaseosos.
Puedes comentar el ratio oxidante-comburente.
Sí, alrededor de 3,4 como todos los motores en este rango.
¿Cuántas cámaras de combustión tendrá el Arcos?
24, tendrá ese número porque cada una de las cámaras tiene 12,5 kilonewtons de empuje entonces es fácil probarlo así.
También porque de esos 24 es simétrico, y puedes hacer buen CFD y todo, bueno eso es broma. [Referenciando a que el CFD nunca es realmente una tarea fácil].
No, pero así podemos separarlo en cuatro sectores, en cada uno habrá una cámara con actuadores lineales que permitirán realizar el TVC [control de empuje vectorial, por sus siglas en inglés].
PLD Space, la otra gran empresa de cohetes española, ha trabajado en el Miura 1, un lanzador suborbital. ¿Vosotros habéis pensado o habéis buscado algún tipo de saltador de baja cota o pruebas de fuego verticales para vuestros motores?
Lo hemos pensado muchas veces la verdad y al final el problema es el dinero. Con Demo P1 sí que intentamos buscar a entidades interesadas en ponerlo en un demostrador pero sin éxito. Yo entiendo que es un activo tener un stand vertical porque estás recreando exactamente lo que pasa en el cohete, pero al final, a estas velocidades de flujo, la gravedad no importa.
Entonces, en tu opinión, no es muy importante probar los motores en vertical.
No, excepto las turbobombas. En ellas sí importa la gravedad y hay que probarlas en vertical. En Arcos lo haremos en un banco de pruebas de la agencia espacial francesa que lo permite.
¿Cuál es el límite superior que tenéis con Arcos de construcción? ¿Cuál es el limitante?
Arcos está limitado por los bancos de ensayo que hay en Europa. Debido a su modularidad y que el aerospike cuanto más grande lo hagas mejor, podemos llegar a 2 Mega Newton, que es lo que permite el banco del DLR, el P5.
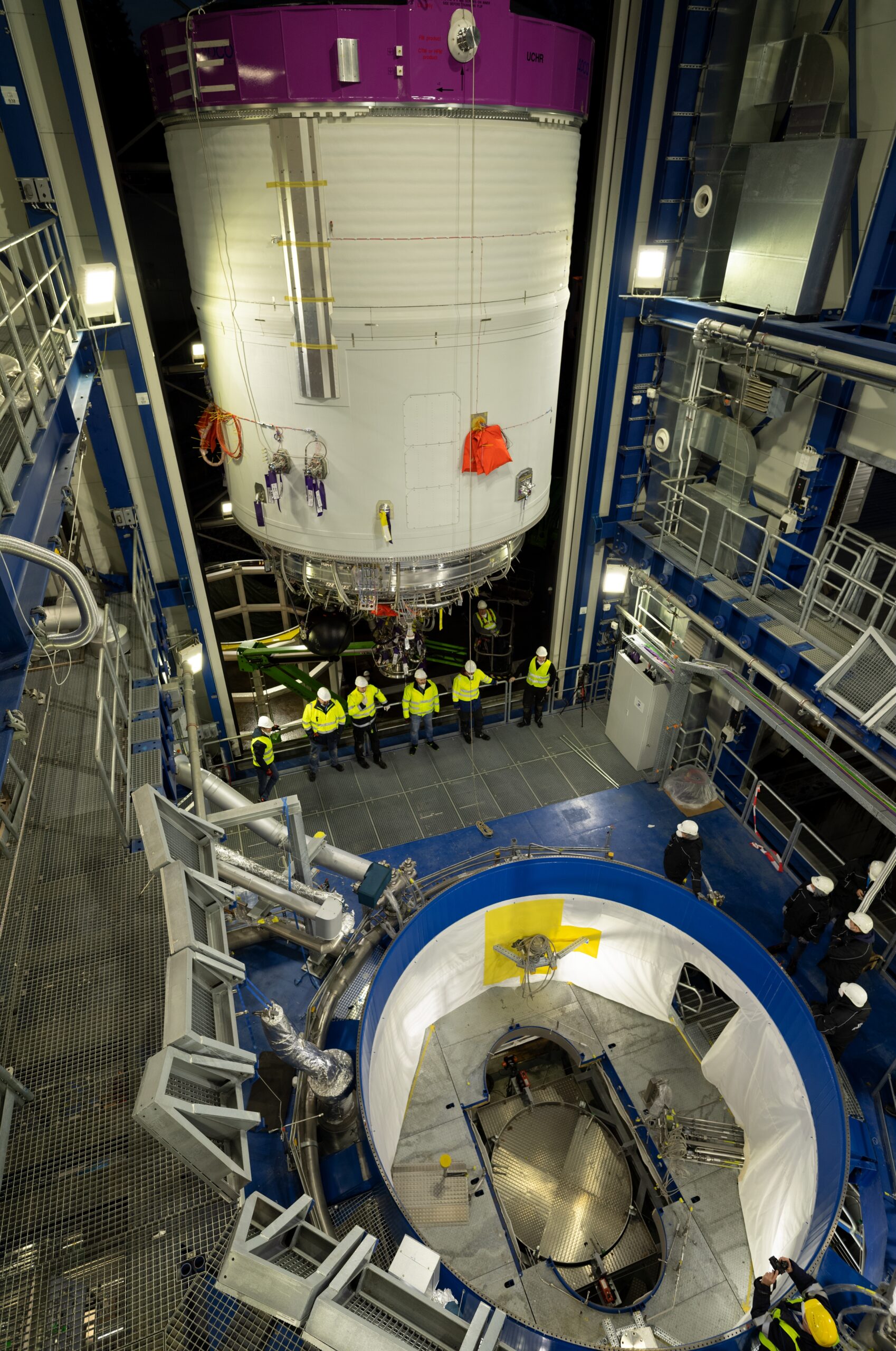
Pasamos también a la segunda etapa. ¿Por qué usar simplemente una tobera convencional, aunque sea sacada del Arcos, en lugar de un aerospike que permitiría una reentrada y reutilización completa del cohete?
Son prioridades, básicamente tiene que funcionar, pronto. Hacer una reentrada hipersónica necesita más tiempo de desarrollar. Nosotros tenemos dos cabezas, una que tiene que desarrollar las cosas pronto y otra que mira al futuro. La segunda cabeza ya piensa en el aerospike en la segunda etapa porque es excepcional. Stoke Space, es una gran inspiración y está haciendo lo que nosotros queremos hacer. La ventaja del aerospike como etapa superior es que puedes maximizar la expansión ratio acortando el motor y también reduces peso de la interetapa.
La otra cabeza tiene que mirar a lo que se puede hacer en un tiempo limitado. Y como tenemos algo modular con Arcos, hemos visto que se adapta muy bien para ser módulos de etapa superior. Así que vamos a reutilizar la misma tecnología que con Arcos.
¿Usarán turbobomba?
Sí, vamos a reutilizar exactamente lo que estamos usando con Arcos. Aunque hemos mirado para utilizar bombas eléctricas, porque para una etapa superior no están mal.
Habéis comentado que vais a usar gas generador, pero, ¿qué otros ciclos de presión habéis planteado?
Tenemos que maximizar el rendimiento y el coste. Hemos ido a por un gas generador. Pero el plan final de la empresa es hacer un motor con un ciclo doble expansivo aerospike.
Con la cantidad de gente que hay con conocimiento de hidrolox, este es el combustible de Europa. ¿Por qué no han apostado por él?
Es una buena pregunta, al final nosotros no estamos cerrados al hidrolox y en el futuro seguramente lo vamos a investigar. Además, está muy de moda y su residuo es agua, pero cuando la empresa empezó el hidrógeno era un reto demasiado grande.
Hay una cuestión con la ignición de la segunda etapa, hay de dos tipos: hot o cold. ¿Cuál optáis vosotros?
Es de las últimas cosas que hemos dicho, será después de la separación [cold, fría].
Pasamos también a preguntas sobre reutilización. ¿Cuál es la parte que más le preocupa?
La reentrada, nunca se ha probado con un aerospike y me imagino que habrá problemas. Al final, a mí no me preocupa que el motor falle, no lo hará porque nosotros lo refrigeramos durante esta fase. Pero después, si hay una fractura, el reacondicionamiento del motor se complica y quizá no se logre retorno económico.
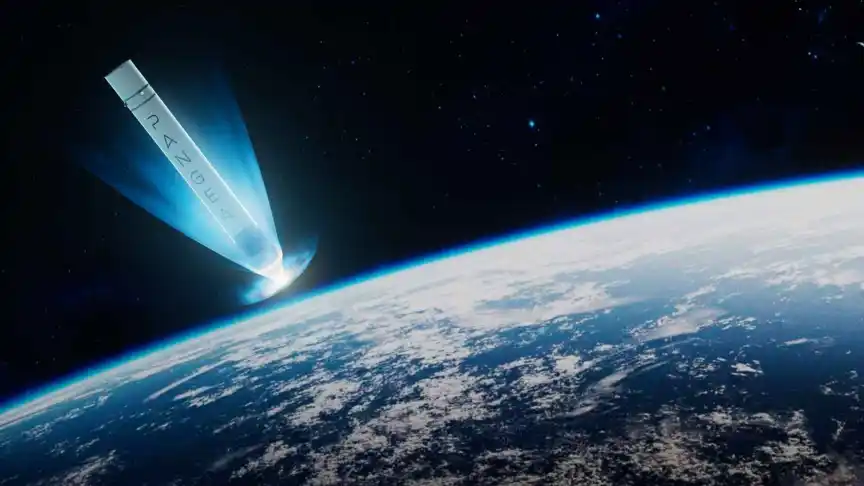
¿Qué número de lanzamientos creen que pueden alcanzar con estos motores?
Tenemos un objetivo de diez, entonces lo estamos diseñando para que aguante cuarenta.
Puedes hablar de las complejidades que supone usar CFD. Porque las simulaciones por ordenador han mejorado mucho, pero siguen sin ser exactas. ¿Qué tipo de problemas os habéis encontrado con ese tipo de cuestiones?
El CFD es delicado, hemos validado muchos de nuestros modelos gracias a las pruebas de Demo P1. Entonces, si tengo que dar un consejo claramente CFD hay que validarlos. Al principio, te puede dar una buena orientación después hay que comprobar.
Recuperando la segunda etapa, el Demo P1 aguantó cinco minutos en ignición. Pero una segunda etapa tiene que quemar mucho tiempo, mucho combustible. ¿Cuánto es el tiempo que vais a tenerlo encendido y cuánto tiempo tendréis que probarlo?
Con Demo P1 se probó 5 minutos porque se acabó el propelente. Con la segunda etapa queremos probar hasta que se rompa. Las simulaciones muestran que podemos hacerlo para treinta minutos tranquilamente.
Entonces, ¿cuánto tiempo va a estar quemando combustible la segunda etapa en un lanzamiento real?
Más de diez minutos.
¿Y la primera etapa?
Dos minutos y medio, más o menos.
Me extraña tan poco tiempo de la primera etapa.
Sí, pero el aerospike lo vamos a utilizar donde es mejor, que es en la parte atmosférica.
¿Cuál será el TWR de la segunda etapa?
Algo superior a la primera, entre 120 y 150. Algo convencional, la segunda etapa no tiene nada de especial.
¿Cómo realizáis la recuperación sin retro propulsión?
Cogiéndolo en el aire. Como Rocket Lab en el Electron, con un helicóptero. Tras muchos estudios hemos llegado a la conclusión que es la mejor forma. [Entre ellos algunos con modelos reales, a escala financiados por la ESA].
El tener que reutilizar un cohete, ¿qué parte es más complicada por la reutilización?
Muchísimas cosas (se ríe). Para empezar el sistema de ignición. Porque podría ser algo pirotécnico porque tú tires una bomba en la cámara de combustión, disparas y ya está. Y no. Eso se tiene que encender muchas veces.
Pero, la más complicada es el sistema de enfriamiento regenerativo. Aquí hay que tener en cuenta muchas cosas. Especialmente la fatiga de ciclo bajo que será como se rompa este motor por primera vez.
Para manejar un cohete hace falta TVC, pero también propulsores de nitrógeno frío o similares, ¿estáis trabajando ya en RCS?
Simplemente tenemos un proveedor externo con motores de este tipo. Son una empresa vieja, y entonces cogemos los propulsores del catálogo basándonos en las especificaciones.
También quiero hablar del motor de 1N que tenéis para propulsión en el espacio. ¿Cómo surgió la idea? ¿Cómo ha sido el proceso de desarrollo?
Muy interesante. La idea surgió porque hemos visto que ahora en los satélites se tienen que mover y tienen que desorbitar en un tiempo muy corto y había mucho mercado para estos sistemas.
Hay otros sistemas, pero son de hidracina que es cancerígena o solo pueden disparar unos segundos antes de parar para enfriarse. Nuestro motor es verde, tiene agua oxigenada y algo más que no puedo comentar y puede disparar por un tiempo virtualmente ilimitado. Es algo único en todo el mundo.
Lo intenté en su momento tanto con Rocket Lab como con los proveedores de la propulsión de Capstone y tampoco quisieron comentarlo, porque hay bastante competencia con el tema de propulsores verdes para cohetes.
Sí, es una alquimia increíble, nosotros para seleccionar el fuel, hemos hecho una comparación entre treinta comburentes diferentes con el agua oxigenada y al final hemos llegado a esto. No es tan fácil como oxígeno y metano, aquí hay mucha más ciencia.
Como ingeniero, ¿fue divertido hallar esa alquimia entre los combustibles y el agua oxigenada?
Sí, porque es como estar cocinando, pruebas una receta, sale mal. Pruebas otra… Aunque hemos hecho pocas pruebas de fuego. Pero sí, es divertido y elegante, el comburente determina como será después el resto del sistema, es muy elegante.
Hemos hablado del empuje, pero la otra métrica mucho menos conocida de los motores tanto aerospike como convencionales de cohete es el ISP, el empuje específico. ¿Puedes comentarnos el de vuestros motores?
Sí, no te puedo dar números, pero te puedo decir que aquí es donde tenemos negocio, en el impulso específico. El aerospike tiene un 15% más de ISP integral sobre la trayectoria dependiendo de los motores que comparamos gracias al expansión ratio.
Puede ser simple, modular y gas generator como el nuestro, pero el impulso específico será brutal y ahí se recupera el rendimiento de la simpleza.
¿Cuál es tu motor favorito?
Sería el XRS-2200, que es el motor aerospike por excelencia.
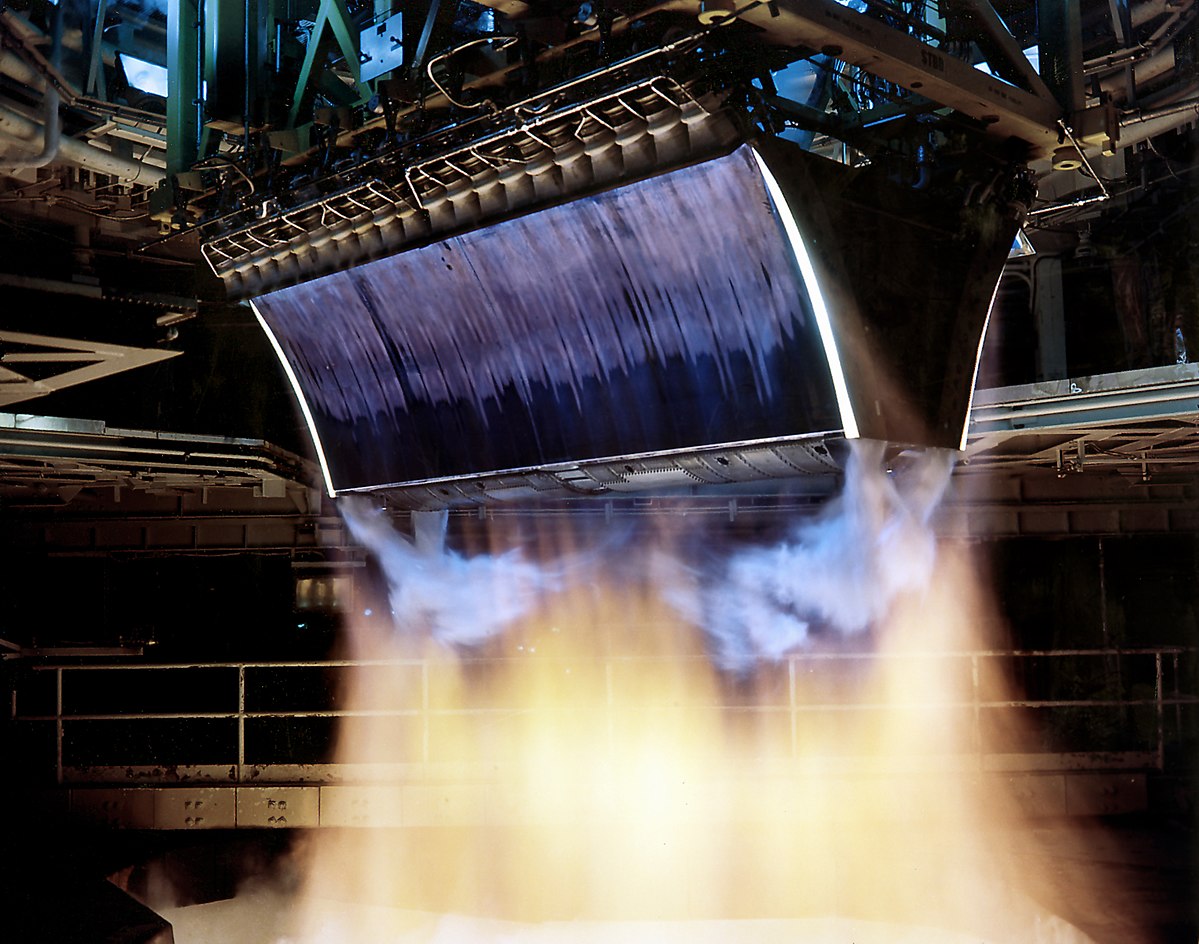
¿Y si señalase uno de la actualidad…?
El Raptor res el rey de todos los motores cohete. Será muy difícil alcanzarlo porque tiene muy buen rendimiento y además es barato.
¿Si no estuvieras en motores aerospike de bio methalox donde le gustaría estar trabajando?
En el Raptor probablemente, en un full flow stage combustión. Diría que es el reto actual.
¿Creen que hay un motor mejor que están desarrollando ahora ahí fuera?
Sí, un motor de más rendimiento sería un dual expander aerospike, que queremos desarrollar nosotros ya que nadie está desarrollando. Eso sería el motor químico de más rendimiento del mundo.
Ya si nos vamos a otras cosas, la propulsión nuclear promete muchísimo, pero claro, también es más complicado, no tanto por cuestiones técnicas.
Especialista en el programa espacial indio.
Universidad de Oviedo.
Comparte esto:
- Entrada
- Haz clic para compartir en Threads (Se abre en una ventana nueva) Threads
- Haz clic para compartir en WhatsApp (Se abre en una ventana nueva) WhatsApp
- Haz clic para compartir en Reddit (Se abre en una ventana nueva) Reddit
- Haz clic para compartir en Telegram (Se abre en una ventana nueva) Telegram
- Haz clic para compartir en Mastodon (Se abre en una ventana nueva) Mastodon
- Haz clic para compartir en Bluesky (Se abre en una ventana nueva) Bluesky